T600 Thickness Gauge
Description of the product
Ultrasonic thickness gauge TG600 has been constructed in order to speed up inspections. The electromagnetic head applied in it allows elimination of the coupling medium, which makes the measurement taking faster and the results more reliable. Due to the contactless measuring the state of the surface does not affect the result. The object being inspected can be corroded, or covered with loose splinters or a paint coating.
Technical parameters
Thickness range | 2 mm – 120 mm |
Resolution | 0,01 mm |
Voltage generation range | 1-4 MHz |
Voltage generation amplitude | 200-600 Vpp |
Acquisition frequency | 50 Msps |
Resolution of the transducer | 12 bit |
Connection | LEMO oB |
Operating temperature | -20/60 °C |
Power supply | 4 AA batteries (R6) |
Dimensions | 138x160x37 |
Advantages of the system
- measurements in high temperatures
- measurements without a couplant
- testing of austenitic welds
- testing with surface waves
- measurements of stresses, loads and grain sizes
- detection of defects and corrosion
KIT CONTENTS
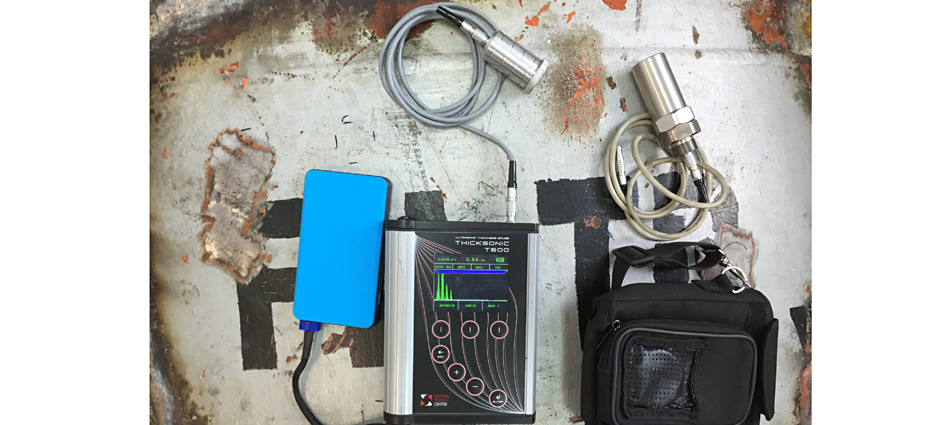
EMAT technology
NON-DESTRUCTIVE ULTRASONIC TESTING METHOD
An alternative method of non-destructive ultrasonic testing that consists in that the wave is generated first in the tested element and not in the piezoelectric transducer. Thanks to this, we can carry out the testing in conditions unavailable for the classical ultrasonic methods.

The EMAT generates ultrasonic waves in the element being tested using two interacting magnetic fields.
The field with a relatively high frequency, which is generated by the electrical coils, acts on the field with low frequency or a static field generated by permanent magnets in order to produce a Lorentz force field in a manner similar the operation of an electric motor.
Introduction of such an interference into the crystalline network causes generation of an elastic wave. In the process of interacting of elastic waves, in the presence of a magnetic field, currents are generated in the EMAT receiver coil circuit.
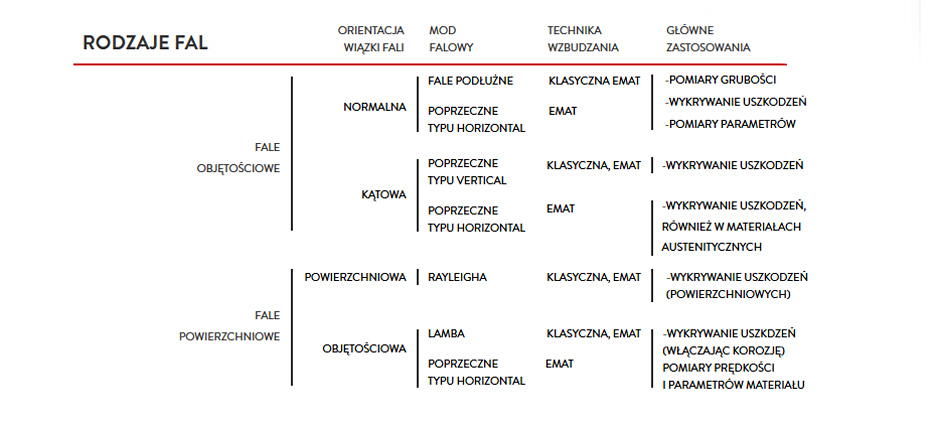
Advantages of the technology
The EMAT technology does not require a couplant to transfer waves, which makes it ideally suited for inspection of objects of high temperatures and for applications in automated inspection stations.
In the case of the EMAT technology, the state of the surface of the tested material does not affect the course of the inspection, which enables inspections of surfaces that are polluted or covered with corrosion or rough ones.
Due to the manner of generating the wave, Snell’s law is not applicable, and the position of the probe against the tested area does not affect the direction of wave propagation. This makes probes easier to operate, especially in automated environments.
- option of signal standardisation for the purpose of automatic and continuous self-calibration
- no couplant or contact with the inspected surface
- the practical distance of the coil from the inspected surface is between 0-3 mm
- a greater distance (even up to 10 mm) can be achieved depending on the material inspected and the devise used and the type of test
- ideal for automated testing and testing in high temperatures
- no impact of the state of the surface on the test result (coatings, oil, corrosion)